Ziele
Das Ziel des Netzwerks ist es mittelständischen Unternehmen den Zugang zur 3D-Drucktechnologie/Produktion zu ermöglichen und sie in der Umsetzung von neuen Produkten und Services zu unterstützen. Ein Alleinstellungsmerkmal des Netzwerks liegt in der Einbindung der Metallpulverentwicklung, die insbesondere für innovative funktionsintegrierende Bauweisen von großer Bedeutung sein wird.
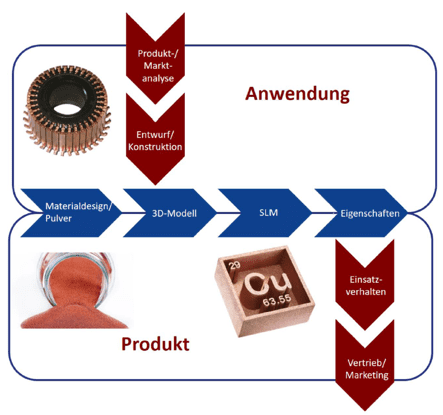
Zu Beginn der Prozesskette steht die Analyse der Betriebsbelastungen des Bauteils. Zur Ausschöpfung des Potentials, dass die Additive Fertigung bietet, ist ein Re-Design des Produktes unumgänglich. Bionische Ansätze haben sich in diesen Teilschritt als sehr hilfreich erwiesen. In den Projekten des Netzwerks InnoMat3D stehen hier Anwendungen aus der Schweißtechnik, der Elektronik und Sonderbauteile im Vordergrund.
Ausgangspunkt eines pulverbett-basierten additiven Fertigungsprozesses ist die Verfügbarkeit von Legierungen, hier Kupfer-, Aluminium-, Nickel-, Eisen- und Titanlegierungen, in Pulverform. Diese können entweder kommerziell erworben werden, wobei die zur Verfügung stehende Bandbreite an Materialien begrenzt ist, oder mittels Gasschmelzeverdüsung (Atomizer) anforderungsspezifisch hergestellt werden. Letzteres erlaubt die unabhängige Entwicklung von gezielt auf die Anwendungsgebiete zugeschnittenen Legierungszusammensetzungen. Durch die Flankierung mit computergestützter Materialsimulation, wie thermodynamische Berechnungssoftware (CALPHAD), besteht die Möglichkeit, die sich potentiell einstellenden Werkstoffmikrostrukturen vorherzusagen und ein computergestütztes Legierungsdesign durchzuführen. Als Ergebnis entsteht ein auf den jeweiligen Aufwendungsfall optimierter, maßgeschneiderter Werkstoff.
Mit Hilfe von CAD-Programmen werden 3D-Modelle des zu fertigenden Bauteils erstellt und in Schichten unterteilt (slicing). Außerdem werden Baustrategien für den anschließenden Fertigungsprozess festgelegt, zum Beispiel die jeweiligen Schichtdicken, Laserleistungen und Hatching-Strategien. Diese Modelle können außerdem als Ausgangspunkt für begleitende Simulationen und Topologieoptimierungen des Bauteils genutzt werden.
Beim Selektiven Laseraufschmelzen (SLM, Selective Laser Melting, auch Laser Powder Bed Fusion LPBF) wird das Pulver im Pulverbett mit einem Laser entsprechend des CAD-Modells schichtweise selektiv aufgeschmolzen. Durch wiederholte Absenkung der Bauplattform und nachfolgende Pulveraufschmelzung entsteht so schrittweise ein additiv gefertigtes Bauteil. Der Erfolg des Fertigungsverfahrens ist dabei maßgeblich von der erzielbaren Prozesssicherheit und den Produkteigenschaften des hergestellten Bauteils abhängig. Durch Post-Processing-Strategien, wie das Spannungsarmglühen oder das heißisostatische Pressen (HIP) zur Reduzierung der Porosität, kann die Qualität der Bauteile maßgeblich verbessert werden, allerdings verknüpft mit einer Kostenerhöhung.
Ein wesentlicher Punkt zur Bewertung eines einsatzbereiten, additiv gefertigten Bauteils ist die Ermittlung der jeweiligen Materialeigenschaften und der Struktur-Eigenschafts-Beziehungen. Entsprechend der jeweiligen Bauteilbeanspruchung müssen z.B. die mechanischen Eigenschaften, das Korrosionsverhalten oder die elektrische Leitfähigkeit eingehend untersucht und charakterisiert werden. Auf Basis der aus den Untersuchungen gewonnenen Erkenntnisse kann das Legierungsdesign aus dem ersten Schritt der Prozesskette gezielt angepasst werden, um schließlich zu einer optimalen Werkstoff-Prozess-Kombination und optimierten Bauteileigenschaften zu gelangen.
Adresse
IEHK – Institut für Eisenhüttenkunde
RWTH Aachen University
Intzestr.1
52072 Aachen
© 2021 InnoMat3D